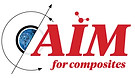

Mission
The mission of this EFRC is to build an AI-enabled inverse design approach for fundamental understanding and integrated material-manufacturing design of advanced polymer composites.
While uncovering these fundamental insights, this EFRC also aims to build Inverse Design Software (InDeS) tools that accelerate the discovery of advanced polymer composites for improved performance and energy-efficient manufacturing, thereby enabling a smaller carbon footprint, lower structural weight, and lower cost.
Research Goals
-
Unravel the fundamental underpinnings of the material-process-microstructure-performance (MP2) relationship via constructing an “Digital Life Cycle” (DLC) that represents a suite of seamlessly linked, experimentally converged, high-fidelity models embracing all stages of a composite component’s life cycle, linking perceived risk from energy consumption to carbon footprint;
-
Leverage physics-informed AI models and build microservice-based cloud tools to enable inverse composites material architecture and manufacturing process design;
-
Inform and validate the DLC and AI models and implement new material and process designs by exploiting innovative material engineering, characterization, and testing methods.
Research Thrusts

The scientific goals will be achieved via three research thrusts as shown in the figure above. Research Thrust I is the DLC representing a suite of seamlessly linked, high-fidelity multiscale models for simulating all stages of a polymer composite’s life cycle, which also integrates uncertainty and environmental-energy-economic (E3) impact quantification. The DLC will enable the generation of a large quantity of high-fidelity data for the development and training of AI models in Research Thrust II. Equipped with the DLC generated data, in Research Thrust II AI modeling and inverse design research thrust, we are developing new AI models to efficiently map the composite materials’ architecture and the manufacturing process to composite components’ performance. Next, we are developing generative neural networks for material and manufacturing process inverse design. In Research Thrust III we are conducting material characterization and testing of mechanical, physical, rheological, and morphological properties at nano-, micro-, and macroscales to inform and validate both DLC and AI models and simulations. We will also implement new/hybrid processes that combine existing or new scalable processing routes to create tailored composite micro and macro structures. Finally, the inverse design is performed by the generative AI models and validated by experimental tests.
News

Professor George Karniadakis won the 2024 G.I Taylor Medal from the Society of Engineering Science (SES)

Professor Srikanth Pilla was named a 2024 Fellow of the Society of Plastic Engineers (SPE).

Professor Yong Huang won the 2024 SME (Society of Manufacturing Engineers) Albert M. Sargent Progress Award.

Interns from North Carolina and South Carolina high schools at SCSU with Dr. Nikunja Swain participated in a Junior ROTC (JROTC) Camp from June 12 to June 16, 2023.

Amit Deshpande won the 1st Place, Technical Poster Presentation at SPE-ACCE Conference, 2023, and the Outstanding Technical Paper Award at CAMX, 2023.
AIM for Composites
Energy Frontier Research Center
Partner Institutions


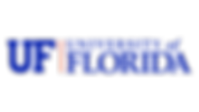



