Testing Services
The CU-ICAR campus buildings house testing equipment and services within the Automotive Engineering program. Resources include a variety of testing capabilities, from metallic and polymeric material characterization to electronic testing of components and full vehicle services. Below are details of the locations, equipment, and services available.
Contact:
Jeremy Barnes
Research Associate & Lab Manager
jbarne9@clemson.edu
Phone: 864-283-7118
Carroll A. Campbell Jr. Graduate Engineering Center
The 90,000-square-foot graduate building houses the automotive engineering graduate program and is the center for systems integration research activities as well as faculty, student, staff offices and conference facilities. The industry-focused and interdisciplinary program utilizes facilities that include full vehicle and engine/powertrain testing. In addition, visiting industry partner offices and visiting faculty offices provide comfortable space for our partners.

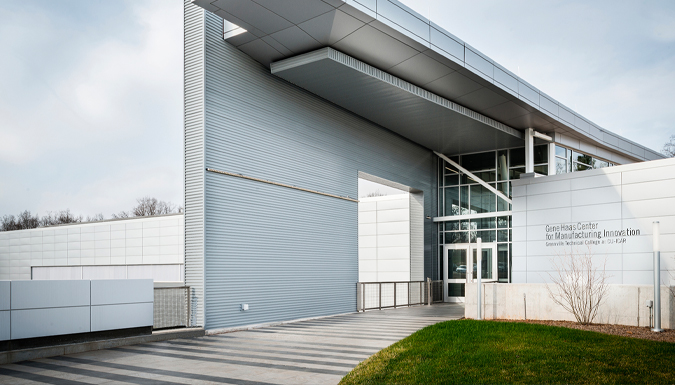
Center for Manufacturing Innovation (CMI)
Greenville Technical College’s Center for Manufacturing Innovation is a state-of-the-art facility designed to provide students with hands-on training in advanced manufacturing technologies. The center features a range of equipment, including robots, 3D printers, and advanced machining tools, as well as classrooms and labs for instruction and research. Through a strategic partnership between the institutions, the CMI is also home to Clemson University’s Vehicle Assembly Center and the Clemson Composites Center.
Testing Equipment and Resources
In addition to the laboratories and extensive equipment available, the technical support staff consists of career technicians with a well-rounded and extensive background in automotive testing and measurement. The technical staff skill set includes machining, mechanics, electronics, instrumentation, servo-hydraulics, measurements, and testing.
-
Renk Labeco 4-Wheel 500 HP Chassis Dyno and Faist Semi-Anechoic Chamber
The Renk system is a low-noise chassis dynamometer housed in a semi-anechoic chamber, making it able to perform driveline noise studies, mileage assessments, sound measurements and all other chassis dynamometer and sound room-related test activities.
Renk Labeco Chassis Dyno Features and Specifications:
- Special noise reduced machine design
- Overhanging roller design with inspection walkway
- Capable of testing of vehicles having FWD, RWD and 4WD
- ABS/ASR car systems do not affect testing procedure
- Includes compensation during test operation for mechanical losses
- Dynamometer drive with speed-and torque-controlled AC-motor (4-Q operation)
- Road load function is fully implemented
- Noise and vibration optimized design
- Temperature range inside test chamber: 10°C (winter) to 40 °C (summer)
- Max front axle weight of test vehicle: 3000 kg
- Max rear axle weight of test vehicle: 2400kg
- Max. total vehicle weight: 5000kg
- Vehicle drive configurations: FWD, RWD, 4WD
- Noise emission 1m above roller at 100km/h: 50 dB(A)
- Max. speed: 200 kph
- Max. power per roller: 95 KW (127 hp)
- Max. total power: 380 KW (510 hp)
- Number of rolls: 4
- Roll diameter: 1274 mm
- Roll width: 650 mm
- Axle base of vehicles under test: 2,100-3,500 mm
- Max outer wheel distance: 2330 mm
- Max inner wheel distance: 1185 mm
- Max. traction force per roll: 4000 N
- Max. roller speed: 850 rpm
- Equivalent base inertia of roller set: 1560 kg
- Roll surface: Smooth machined steel
- Friction coefficient steel to rubber: approx. 0.7 – 0.8
- Balancing quality: (VDI 2060)Q 2.5
- Vehicle cooling airflow: 600 to 30580 m3/hr
- Exhaust suction airflow: 600 to 4080 m3/hr
Faist Sound Room:
- Broad band compact absorber design (no wedges, 350 mm thick)
- Conforms to ISO 3745
- Frequency range 50 – 10,000 Hz
- Room size: 9350 mm long by 8230 mm wide by 4570 mm high
- Door size: 3480 mm wide by 3000 mm high
-
MTS 320 Tire Coupled Road Simulator and Weiss Climate Test Chamber
This system consists of an MTS 320 road simulator with 4 vertical servo-hydraulic actuators to simulate vertical road inputs. The Weiss climate chamber is capable of -40C to +85C operation and a relative humidity range of 15% – 95%. This equipment also includes an MTS SWIFT wheel force transducer, a SoMat in-vehicle data acquisition system, all of which will be used to develop real time test inputs based on actual on-road or proving ground measurements. This test facility will support activities such as squeak & rattle testing, vibration testing, structural durability testing, suspension characterization testing, and fastener testing. Having the road simulator in an environmental chamber allows for many unique testing possibilities.
MTS 320 Road Simulator Features and Specifications:- Maximum total vehicle weight: 5000 kg
- 35 KN actuators, 250 mm stroke, 340 L/min flow rate servo-valves
- Moveable floor and actuators accommodate wheel bases of 2,450 mm to 3,300 mm (Mini-Cooper to Humvee)
- Maximum velocity of 3,500 mm/s and maximum acceleration of 17 G
- Drive-on system (actuators located in a pit)
- SWIFT 30T Wheel Force Transducer System for measuring road inputs
- On-vehicle data acquisition system (Somat EDAQ)
Weiss Environmental Chamber Features and specifications:
- Climate chamber dimensions: 8,750 mm, 6,475 mm and 3,350 mm
- Door opening: 3,023 mm wide by 2,438 mm high
- Temperature range: -40 C to 85 C
- Humidity range: 15 percent to 95 percent
- Heating rate (average): 1.3 C/minute with 3,000 kg vehicle in the chamber
- Cooling rate (average): 0.9 C/minute with 3,000 kg vehicle in the chamber
-
FEV 500 HP Engine Dyno Test Cell
A containerized and expandable facility, this system accommodates testing of performance, engine durability and components, emissions, fuel, catalysts, and engine mapping and calibration.
Features and Specifications:- Containerized test facility
- Test cell management system for data acquisition and control
- Rated Power: 428 kw (580HP)
- Rated Torque: 950 N-M
- Rated Speed: 4,300 rpm
- Maximum Speed: 9,000 rpm
- Inertia: 0.81 kg m2
- Speed Gradient: 9,000 rpm/sec
- Ultra low vibration and noise
- Transient cycle capability (HDDT, FTP 75)
- Integration of Dyno drive, throttle actuator and torque flange
- Quick change pallet
- Entire measurement equipment on pallet (including ECU)
- Standardized connections to drive shaft, exhaust system
- Manual quick connectors for media, measurement equipment, electrical
- Capability of commissioning outside test cell
Modular design 19-inch Rack Mount Instrumentation Package including:
- 16 Analog voltage inputs, 16 outputs
- 16 “J” Type thermocouple inputs
- 16 “K” Type thermocouple inputs
- 16 pressure transducers
- 32 Digital inputs
- 32 Digital outputs
- 12 Frequency inputs
- High transmission reliability
- CANopen Interface
- High flexibility
- Expandability
-
Advanced Powertrain (APT) Laboratory
The first APT lab test cell was constructed in 2016, with the second test cell finishing construction in 2022 and final test cell due to complete in 2023. Dynos in A and C are double ended for dual engine/motor set-ups, all dynos are asynchronous. Each Test cell:
- Lab is equipped with INCA/ETAS calibration software, Vector CANBUS hardware and software for CAN communications
- Each test cell is outfitted with temperature (type K thermocouples), high speed analog inputs, digital input and outputs, pulse counters
- Ability to use Yokogawa 6 channel power analyzer
- E-Motor base, headstock, and spindle bearing to mount e-motors in 120 A and C
- SESAM FTIR 2 channel exhaust gas analyzer
- Cambustion exhaust gas analyzer
- MicroIFem Piezo amplifier for combustion pressure signals
120A Test Cell is a 600 hp (440 kW) dyno / 1,377 ft-lbs (1,867 nM) / 2,250 RPM nom 8,000 RPM max
- High Speed gradient by optimized low inertia
- HBM T04B 3KNM Torque Flange
- Driveline safety guards
- Isolated Bed plates 6500mm x 2500mm
- Dynamometers are controlled via AVL PUMA2 systems
- Fuel flow range up to 150 kg/h
- Fuel (Diesel, Gasoline, Alcohols, Biodiesel)
- Coolant IC Engine power range 200kW to 600kW (450kW nominal cooling capacity)
- Coolant control temperature range (70 to 120°C)
- Indimaster Advanced 672 Gbit interface for high-speed combustion analysis
120C Test cell 750 hp (560 kW) dyno / 2,212 ft-lbs (3,000 nM) / 1,759 RPM nom speed 6,000 RPM max speeds
- High Speed gradient by optimized low inertia
- HBM T04B 3KNM Torque Flange
- Driveline safety guards
- Isolated Bed plates 6500mm x 2500mm
- Dynamometers are controlled via AVL PUMA2 system
- Conditioned air supply system (15 to 70°C)
- Air inlet mass flow measurement range of 40kg/h to 2900kg/h
- Fuel flow range to 250 kg/h covers range from small single cylinder up to 1250kW engines.
- Fuel (Diesel, Gasoline, Alcohols, Biodiesel)
- Coolant IC Engine power range 200kW to 600kW (450kW nominal cooling capacity)
- Coolant control temperature range (70 to 120°C)
- Charge Air Cooler (CAC) temperature range (5 to 225°C)
- MicroIFem Piezo amplifier for combustion pressure signals
120D Test Cell 50 hp (250 kW) dyno / 368 ft-lbs (500 nM) / 4,800 RPM nom 15,000 RPM max
- 120D E-Storage is a combined Battery Tester, Battery Emulator / Simulator 250kW, 1200 V output voltage, 600 A output current
- Torque Flange T12HP 1 kNm up to 20 krpm speed
- Intermediate Bearing Support for driveline support and attachment up to 22 krpm speed capacity
- Coolant e-Motor 20kW nominal cooling capacity
- Coolant control temperature range (10 to 140°C)
-
R&D Machine Shop
A well equipped machine shop with turning, milling, drilling, sawing, and welding capabilities is located within the Campbell Center.
Note: Our machine shop serves primarily for internal and external research and development purposes. At this time we are not accepting production orders.Machine Shop Equipment:
- GANESH GT 18-40 CNC Lathe with Fanuc Series Oi-TF
- ACER 3VKH E-Mill (3 Axis / CNC or manual operation)
- Lincoln 300 MIG Welder
- Lincoln TIG Welder
- Wilton 7040 Horizontal Band Saw
- Parma-Dake 20” Vertical Band Saw
- Wilton 2221VS 20” Floor Drill Press
- Dake 25 Ton H-Frame Hydraulic press
- Wilton 4200A Belt and Disc Finishing Machine
- Bench Grinders
- Sand Blaster
-
Data Acquisition and Instrumentation Services
The Campbell Center is equipped with a full range of instrumentation and portable data acquisition tools for the collection of engineering data on the road, in the field, and in the laboratory. The staff includes one engineer and three technicians with extensive industry experience. Capabilities and resources are outlined below and include the following:
Data Acquisition Equipment:
- Two SoMat EDAQ multi-purpose data acquisition systems with a total of 88 measurement channels including 40 strain gage/bridge channels and 8 thermocouple inputs.
- Mueller MKII 28-channel data acquisition and analysis system with PAK software for NVH measurement and analysis projects.
- Miscellaneous National Instruments equipment and instrumentation
- dSpace microautoboxes and HIL simulator platform
- DAQ systems for NVH testing:
- Siemens Scadas systems (full use of SimCenter TestLab Software:
- (2) 2 slot systems configurable for up to 32 input channels
- 8 ch NVH with EtherCat
- 24 ch V/ICP Inputs
- 8 ch thermocouple inputs
- (1) Scadas XS Compact 12 ch system
- Siemens Scadas systems (full use of SimCenter TestLab Software:
Sensors and Measurement Capabilities:
- Full capabilities to instrument vehicles for on and off road measurements
- Complete strain gage installation and measurement services
- DC and modal accelerometers
- Impact hammers for modal analysis
- Type I microphones (7) and Larson Davis 831 sound level meter.
- Custom strain gage based load cell design, fabrication, and calibration capabilities
- Miscellaneous displacement transducers, gear tooth sensors, optical tachometers, thermocouples, angular rate sensors, DC current transducers, etc.
- Vehicle bus and GPS measurements
Data Analysis Software:
- MATLAB
- Dadisp
- SoMat Infield
- Mueller BBM PAK 5.5
- University of Cincinnati XModal
- Data Physics SignalCalc Mobilyzer Dynamic Signal Analyzer
-
Clemson Composites Center
Capabilities encompass a wide range of applications, from material synthesis and characterization to engineering and manufacturing services. Ongoing projects run the gamut from fundamental science to translational projects, all driven by the industry’s need for a more sustainable future. The Center offers state-of-the-art equipment and infrastructure needed to develop, transform and commercialize cost-effective, efficient and sustainable technologies related to composites and lightweight materials design, processing, manufacturing, characterization and testing. The Center also offers full-scale prototyping and short-volume production runs for advanced composites and polymer components.
For more information about available equipment and services, visit the Clemson Composites Center website. Billing rates are available upon request.
Contact: composites@clemson.edu -
Clemson Vehicle Assembly Center (CVAC)
The Clemson Vehicle Assembly Center is an environment to co-educate researchers, engineers, technicians and workforce in a realistic environment, building learning, confidence, teaming and leadership. The core of CVAC consists of a 3-station vehicle assembly line with lighting, sound, velocity, position, and height control. Specifications include:
- Human-robot cooperative subassembly systems
- Universal Robots UR16, UR10, and UR3 actuation arms with different sensing and end effectors
- Siemens SIMATIC S7-1500 controllers
- Suite of Atlas-Copco data-enabled fastening tools
- Networked environmental sensors: CO2, CO, VOCs
- IBM rack server closed local cloud system for data management
- Embedded systems laboratory
-
Clemson OpenCAV
The OpenCAV group is developing a novel modular, open-architecture, open-interface, and open-source-software based research instrument comprised of- Augmented Reality (AR) based simulation to facilitate Simulation- based-Design (SBD) of hardware (e.g. sensor-suites) and software (e.g. algorithms) for a range of Connected and Automated Vehicle (CAV) applications; and
- Physical real-time hardware-in-the-loop validation on a full-scale vehicle retrofitted with advanced sensing, drive-by-wire, perception, connectivity, computation, and control modules.
Watch a video overview about the system, or watch a hardware overview.
Download the OpenCAV Spec Sheet
Contact: Dr. Venkat Krovi
-
Image Gallery
Renk Labeco 4-Wheel 500 HP Chassis Dyno and Faist Semi-Anechoic Chamber
MTS 320 Tire Coupled Road Simulator and Weiss Climate Test Chamber
FEV 500 HP Engine Dyno Test Cell
Advanced Powertrain (APT) Laboratory – Control Center
Advanced Powertrain (APT) Laboratory – Test Cell A
Advanced Powertrain (APT) Laboratory – Test Cell B
Advanced Powertrain (APT) Laboratory – Test Cell C
R&D Machine Shop
Data Acquisition and Instrumentation Services